A evolução da matriz energética mundial traz à tona desafios técnicos que exigem uma readequação das estratégias de projeto. Neste artigo falaremos sobre o fluxo reverso em transformadores e o seu impacto no projeto térmico e no isolamento do equipamento e algumas estratégias para identificar e atenuar os efeitos deste fenômeno.
De um modo geral, do ponto de vista de funcionamento do equipamento, a ocorrência de um fluxo reverso pode causar uma deformação na corrente do equipamento (harmônicas), alterando o perfil de distribuição e a amplitude de perdas no equipamento. Este fenômeno pode ser ainda mais significativo para transformadores multi-enrolamentos ou dotados de enrolamentos de regulação (comutador a vazio ou sob carga).
Essa alteração ocorre tanto nas perdas nos próprios enrolamentos quanto nas perdas nas partes metálicas de fixação da parte ativa ou do tanque. Isso ocorre porque o fluxo reverso altera as características da corrente dos enrolamentos e, consequentemente, modifica também a distribuição do campo magnético disperso da máquina, causando as perdas parasitas.
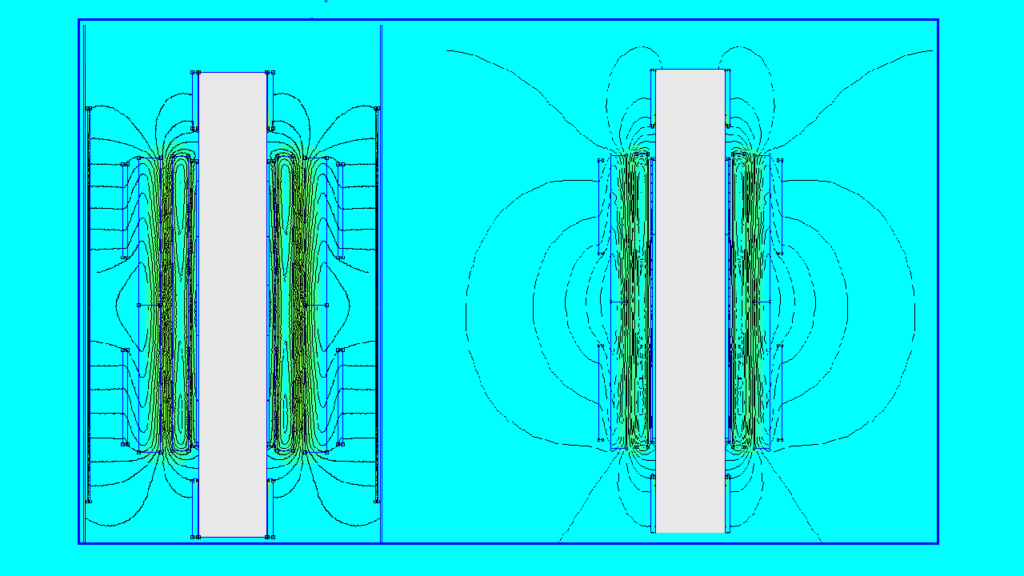
Na prática, o que pode acontecer é um aumento na temperatura de operação do equipamento, principalmente na temperatura do topo do óleo e na temperatura do ponto mais quente do enrolamento (hotspot).
Então, surge o questionamento: é possível acompanhar ou verificar esta condição nos transformadores em operação?
Do ponto de vista de alteração no valor total de perdas total, é relativamente simples de diagnosticar qualquer alteração, principalmente porque vai alterar a elevação da temperatura do topo do óleo. Como este parâmetro, normalmente, é medido continua e diretamente no equipamento em operação, quando são atingidos valores pré-definidos podem ser acionados os alarmes e as proteções correspondentes.
Entretanto, quando se trata de alteração da distribuição da elevação de temperatura do ponto mais quente do enrolamento ou das partes metálicas internas pode surgir um perigo oculto. Isso ocorre porque, infelizmente, esses pontos são mais difíceis de monitorar, principalmente quando se trata de transformadores mais antigos que foram fabricados sem sistemas de medição direta de temperatura para o enrolamento ou ferragens (atualmente realizado com utilização de sensores de fibra ótica).
Aqui cabe uma observação que alguns clientes que têm monitores de temperatura podem ficar na dúvida se estes equipamentos são capazes de identificar essa alteração do perfil de distribuição de temperatura no enrolamento. Neste caso não é possível identificar este aquecimento pontual com os monitores de temperatura que funcionam de maneira indireta.
Isso acontece porque ao contrário do monitor da temperatura do topo de óleo, que tem como princípio de operação a medição direta no transformador, a medição da temperatura do enrolamento é realizada de maneira indireta, ou seja, estes monitores utilizam de parâmetros pré-determinados e do valor instantâneo da corrente para determinar um valor de elevação de temperatura médio para o enrolamento. Por isso, não são capazes de identificar de maneira eficaz se a alteração da temperatura acontecer em uma única e isolada região do enrolamento, ou seja, esta região pode ficar praticamente “invisível” para estes monitores indiretos de elevação de temperatura (aqui são incluídos os monitores indiretos analógicos da foto acima e até mesmo os digitais que são mais atuais).
Retomando o assunto principal deste artigo: é importante ressaltar que a alteração do perfil térmico não vai levar o equipamento à falha imediata, mas, com certeza, vai causar um dano pontual no isolamento e vai diminuir a vida útil projetado para o ativo.
Resumidamente o que ocorre é o seguinte:
O projeto magnético (distribuição de corrente, campo magnético e perfil de perdas) altera o projeto térmico (distribuição da temperatura) que tem influência direta e fundamental no projeto elétrico do isolamento (perda da capacidade de isolamento pontual) levando o equipamento à falha elétrica (ruptura total do isolamento e descarga elétrica).
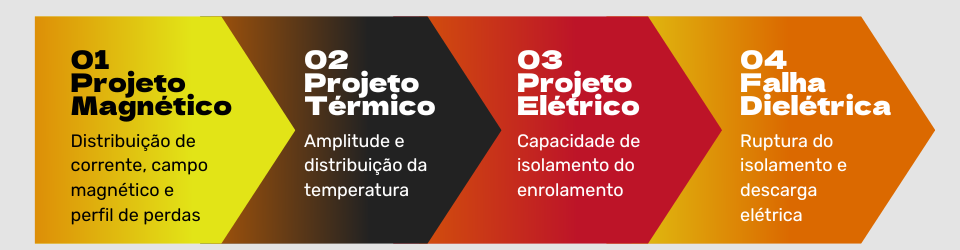
Um fluxo reverso no transformador pode causar uma alteração da distribuição do campo magnético e um aquecimento pontual dos enrolamentos e, com isso, causar uma degradação do isolamento desta região, gerando as condições podem causar a falha dielétrica do equipamento.
O projeto magnético (distribuição de corrente, campo magnético e perfil de perdas) altera o projeto térmico (distribuição da temperatura) que tem influência direta e fundamental no projeto elétrico do isolamento (perda da capacidade de isolamento pontual) levando o equipamento à falha elétrica (ruptura total do isolamento e descarga elétrica).
Obviamente não é possível generalizar esta conclusão (um pouco trágica): nem todo transformador exposto a um fluxo reverso vai falhar precocemente. O objetivo deste artigo é discorrer sobre este tema para levantar alguns pontos importantes que interferem neste comportamento e que podem ser avaliadas para determinar a gravidade desta condição. Algumas das principais são listadas a seguir:
- Características de eletromagnéticas de operação do transformador;
- Potência e tensão do transformador;
- Disposição e geometria construtiva dos enrolamentos;
- Características construtivas da parte-ativa completa e tanque;
- Quantidade e distribuição do fluxo magnético disperso;
- Nível de elevação de temperatura do enrolamento (fator de hostpot);
- Elevação de temperatura do óleo de projeto;
- Condições de carregamento;
- Preservação do isolamento.
E, por último: Como acompanhar esta condição nos transformadores?
Para os transformadores com medição direta de temperatura nos enrolamentos, como a utilização de fibra ótica, por exemplo, a questão é simples porque se trata de observar os valores de elevação de temperatura do enrolamento ou das ferragens deste transformador durante as diversas condições operação.
Para os transformadores sem medição direta de temperatura, a melhor alternativa seria aumentar a frequência da realização das análises de gases dissolvidos no fluido isolante (pode ser utilizado como referência um período de 6 meses ou menos entre cada amostra, dependendo da aplicação e condição de operação do transformador). Nestes casos, um aquecimento pontual no enrolamento vai causar uma degradação do papel isolante e, com isso, gerar principalmente o gás chave Monóxido de Carbono (CO) e Dióxido de carbono (CO2), além de outros gases associados ao aquecimento também do óleo.
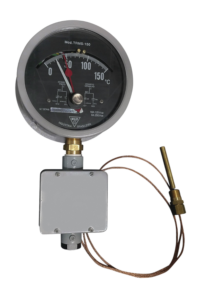
Por fim, cabe o comentário de que, com bases nos dados obtidos direta ou indiretamente, é possível determinar algumas condições para preservação da vida útil do equipamento. Para isso poderia ser utilizado, por exemplo, ferramentas de simulações numéricas baseadas em elementos finitos para determinar a distribuição das perdas e da elevação de temperatura no equipamento. Com isso poderia ser atribuído um limite de potência de operação ou uma otimização o sistema de refrigeração natural ou forçada para controlar a temperatura e prevenir o envelhecimento acelerado do isolamento do transformador que poderia levar a uma falha dielétrica precoce o que, além de causar o prejuízo atribuído ao ativo, pode impactar nos índices de confiabilidade do sistema elétrico.
Texto elaborado por: Odirlan Iaronka
Contato: [email protected]